A webinar on HSE best practices, risk management and audit in mines in North Ontario (Canada) and other countries was attended by HSE practitioners from Russia, Ukraine and Kazakhstan. The event featured presentations by HSE professionals from Australia, UK, USA and Workplace Safety (Canada). The attendees took great interest in the methods of correcting behavioral patterns, incentives for accident-free operation, new understanding of safety barriers, KPIs for preventing accidents and injuries. Many webinar participants expressed 100% satisfaction with this training course in their feedback forms.
CALL FOR PRESENTERS
Transeuropean is holding series of webinars for mining engineers and other industry professional on geology, resources reporting, processing, water and tailings management, safety in surface and underground mining operations and automation. This is an excellent opportunity to showcase one’s capability, networking and business development. If you are interested to present in Zoom to groups of 20-25 senior technical executives and engineers please get in touch with Natalia Kirsanova, director on 07768 081863 or office@transconf.com
Terrafame Mine in Northern Finland – High Efficiency, Profitability and Ecology
A group of geologists, enrichment technologists and occupational safety and health specialists from Russia, Kazakhstan and Ukraine attended an intensive training seminar with technical visits to Helsinki and Talvivaara.
At the Terrafame open-cast polymetallic mine (formerly Talvivaara), the delegation studied the organization of mining operations and examined the heap bioleaching zone, where the gold extraction process takes place, even in severe frosts, at a temperature of 40-60C due to the exothermic reaction in the heap. The technological scheme and equipment of the crushing line was disclosed in detail in the reports of Sandvik and Outotec specialists.
The delegates for the geological section from MMC Norilsk Nickel, Norilskgeology and AGD Diamonds examined issues of quality control of geological exploration and core samples (speaker Dr. Julia Cherepanova), studied the On-Line Mine technology of the Finnish company IMA Engineering – collection and analysis in real time data on the metal content during production activities from core, drilling waste and from ore on a conveyor belt and visited the Finland Geological Survey GTK, founded in 1885 by decree of Emperor Alexander III.
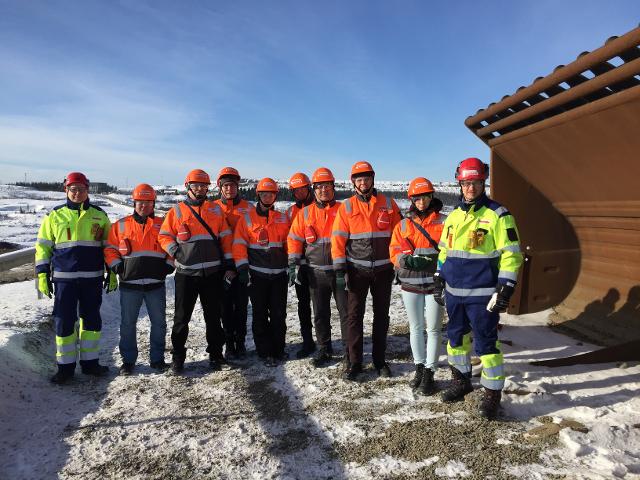
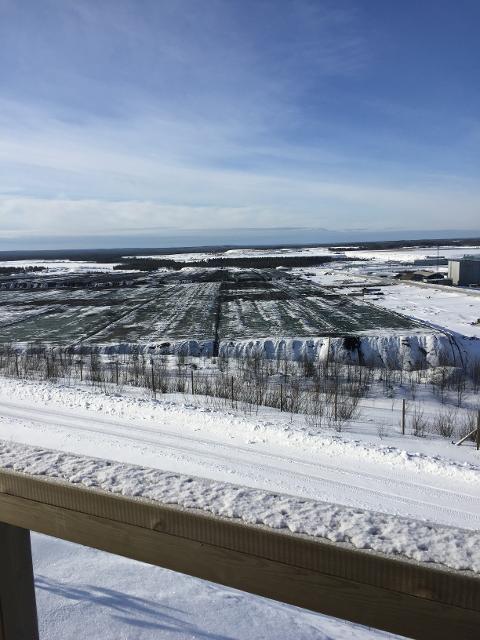
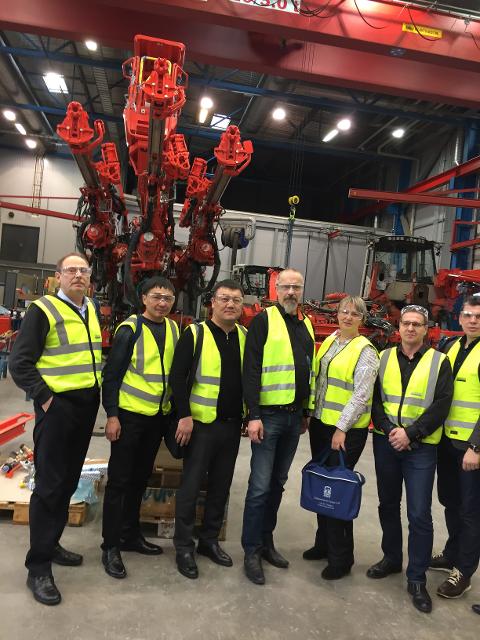
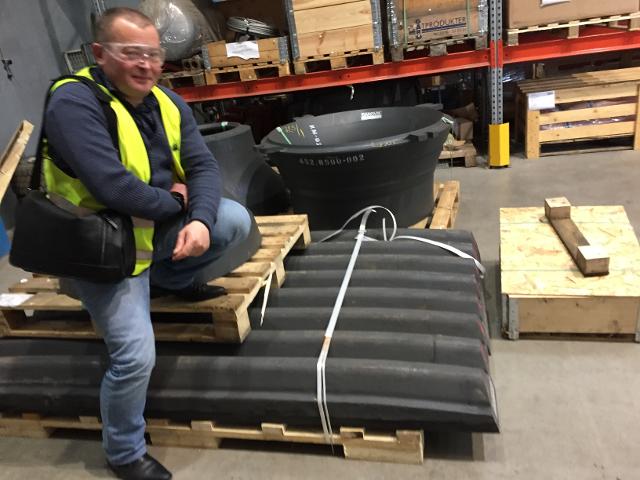
“Rosmorport” visits Europe’s largest ports of Antwerp, Rotterdam and Hamburg.
On February 3-8, a delegation of 21 senior managers of the “Rosmorport” visited the ports of Antwerp, Rotterdam and Hamburg in order to familiarize themselves with the efficient operation and development projects at those largest port complexes in Europe. The program of the Rosmorport visit was extremely busy and included discussion of tariff policy and port charges, development and modernization of ports, ensuring maritime safety, environmental management, construction of new terminal complexes, modelling and calculation of cargo flows.
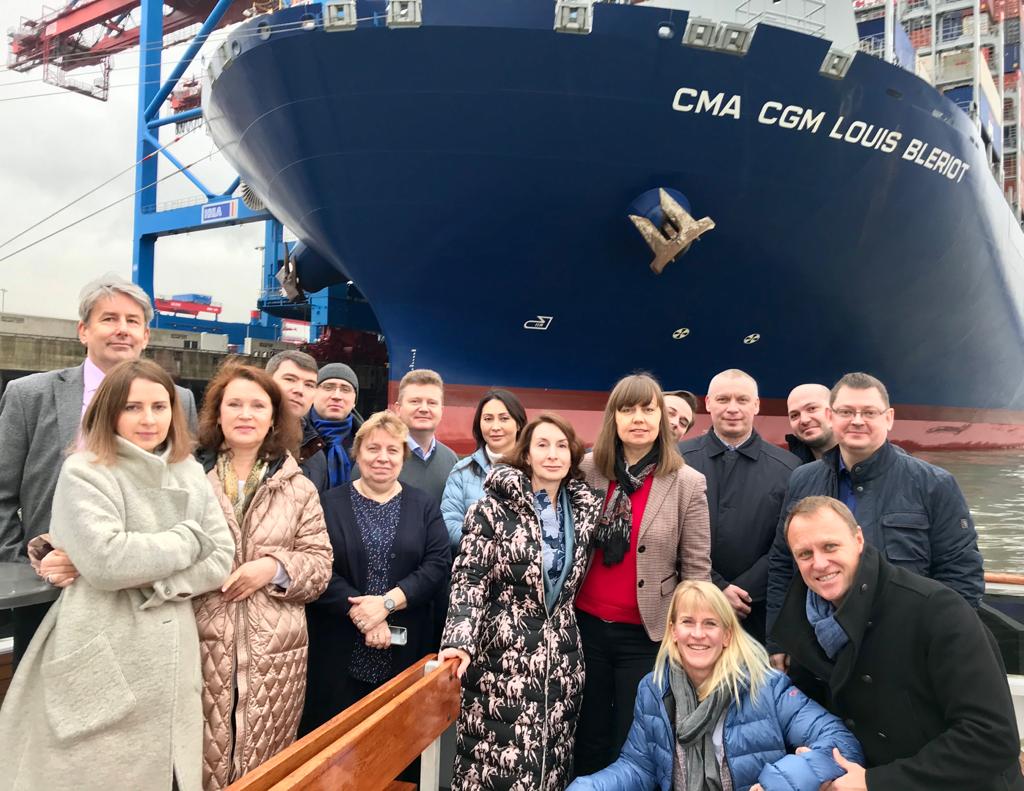
During meetings with colleagues from European ports special attention was paid to digitalization, in particular the development of an integrated digital system for all participants in the transportation process, simplification of cargo declaration and customs procedures.
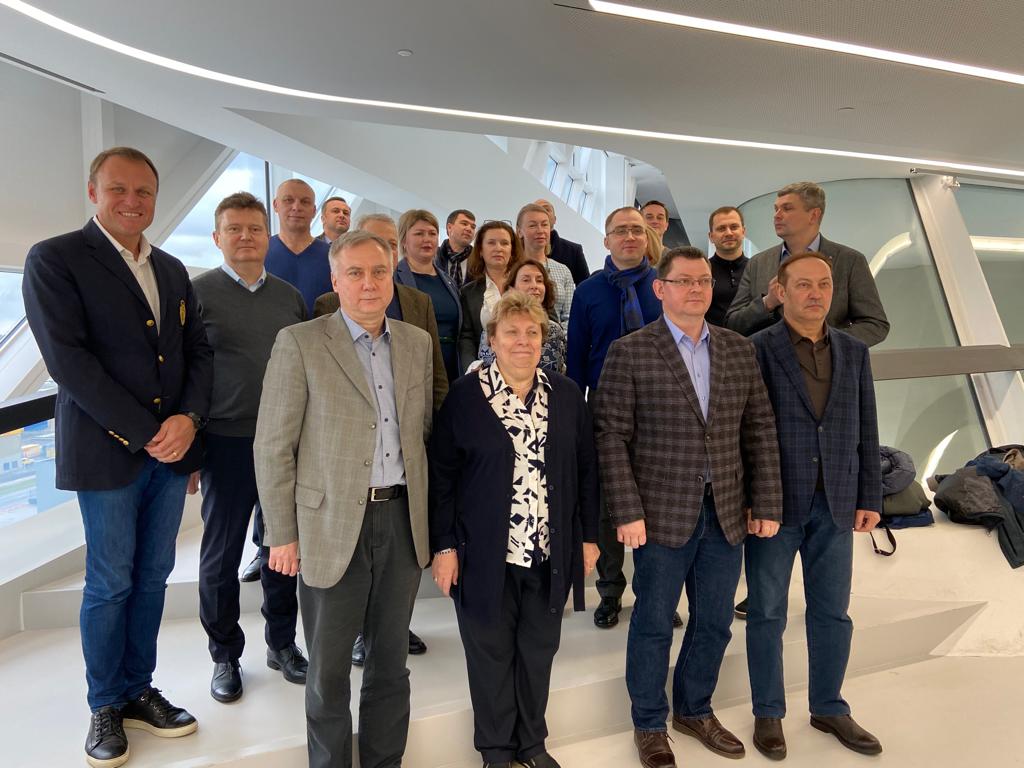
The delegation was introduced to the activities of pilotage services and the management of the safe movement of ships in the port, the design and undertaking of dredging operations and advanced methods of port locks and jetties. In particular, they discussed the Maasvlakte 2 project to expand the port area of Rotterdam.
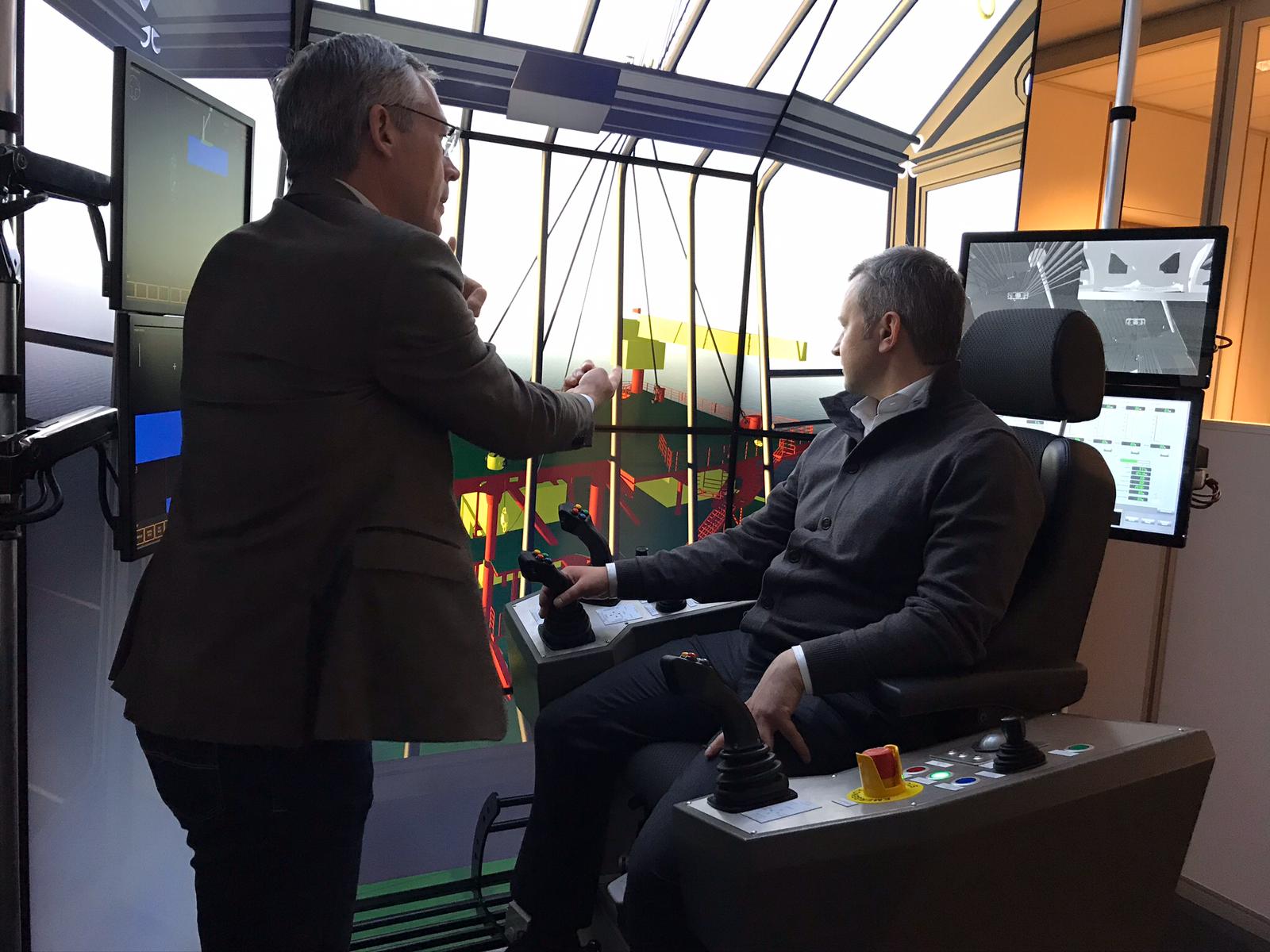
Workshop in Australia November 4-9, 2019: Learning from the experience of remote control, digitalization and automation of mines.
A seminar of the Trans-European Center in Australia in Perth on the topic: “The experience of Australian mining companies in the automation of production was successfully held from November 4-9.
The event was attended by representatives of Altynalmas, EuroChem, Nordgold, Norilsk Nickel, Apatit, VIST-Group, Lake Mining Company, Polyus-Project and Ferrexpo.

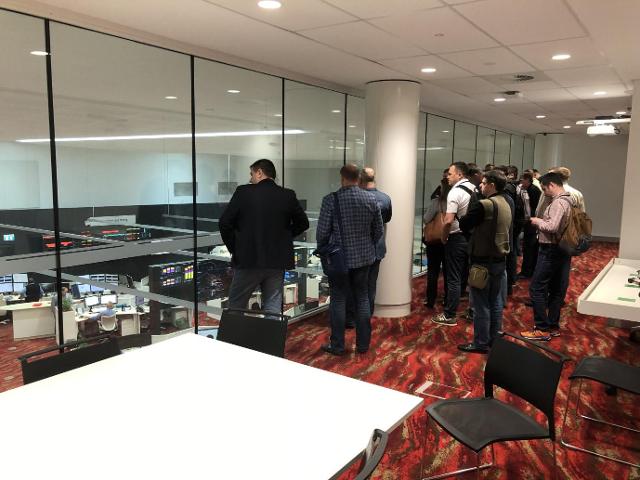
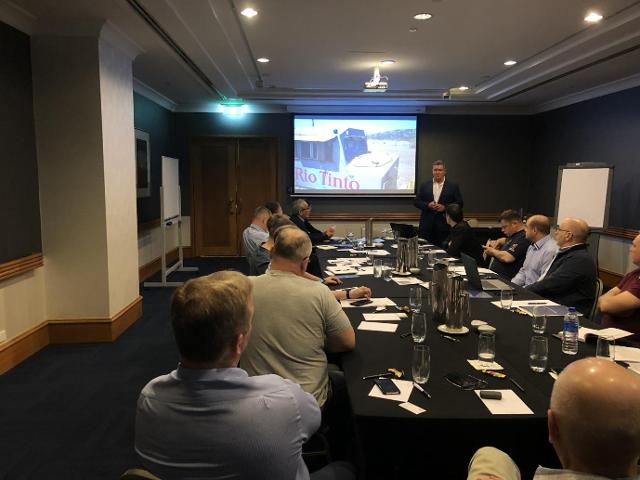
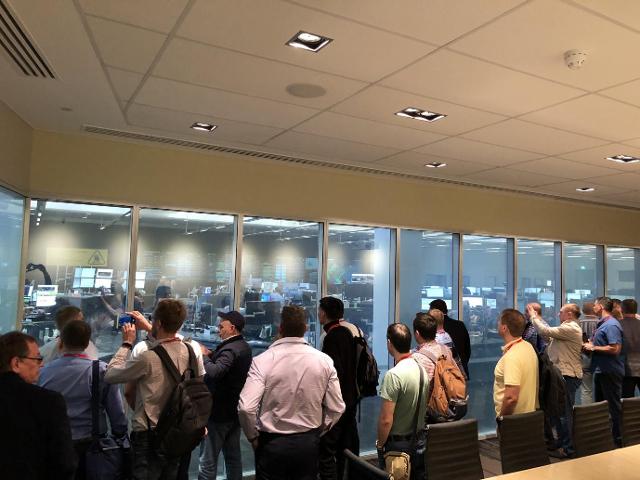
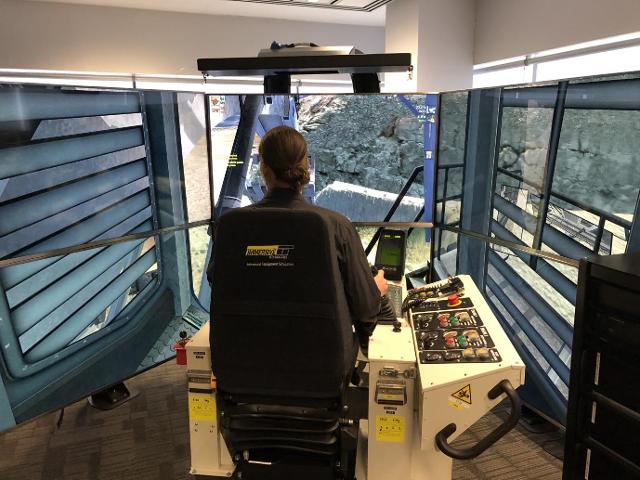
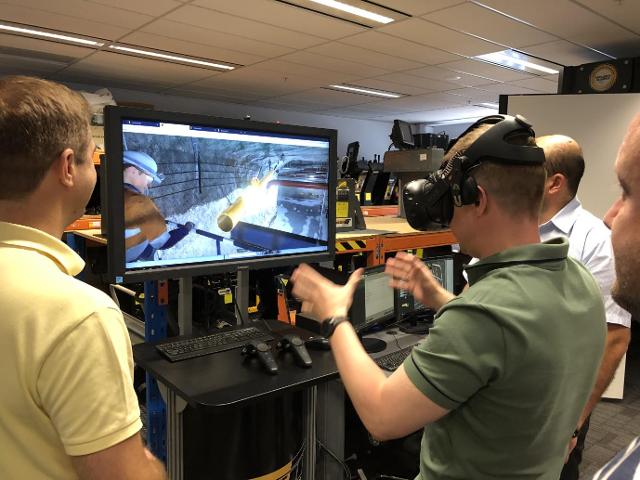
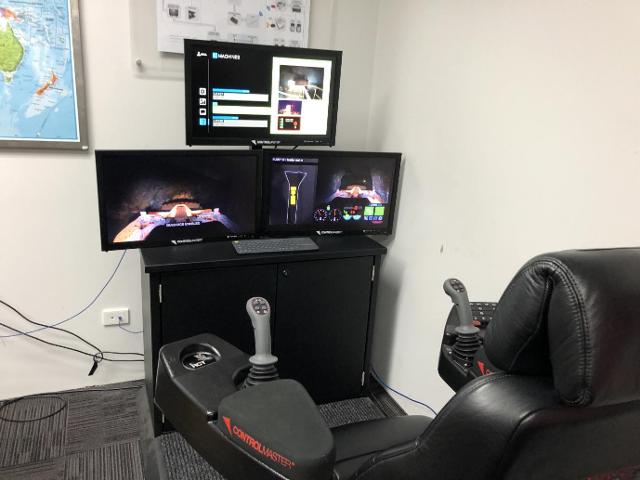
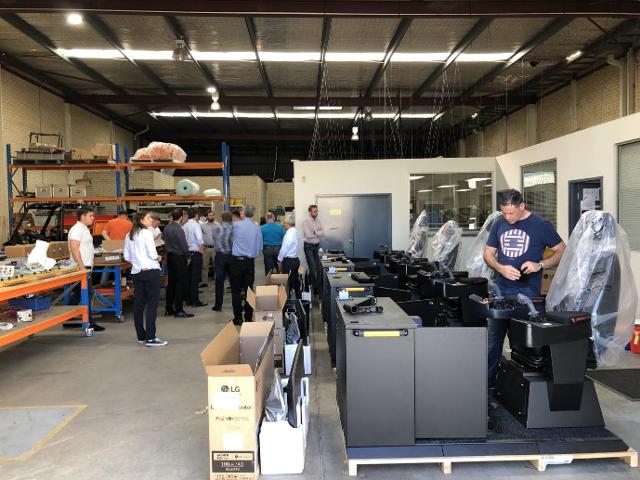
Visits to Canadian mining companies in Toronto and Sadbury
The Transeuropean Centre successfully held a seminar and a series of technical visits for mining companies in Canada on September 9-14, 2019. Mining engineers from more than 15 Russian and Kazakhstan companies including Alrosa, Nordgold, SPB Mining, Uralkali, Arctic Palladium, Severstal and many others visited the Porcupine gold mine operated by the Canadian company GOLDCORP in Timmins and several technology companies and centres in Sudbury, Ontario. A large mining cluster is situated in Sudbury where nickel, molybdenum and other polymetallic ores have been mined for over 100 years.
A series of meetings on innovations in the mining industry took place in Toronto and Sudbury.
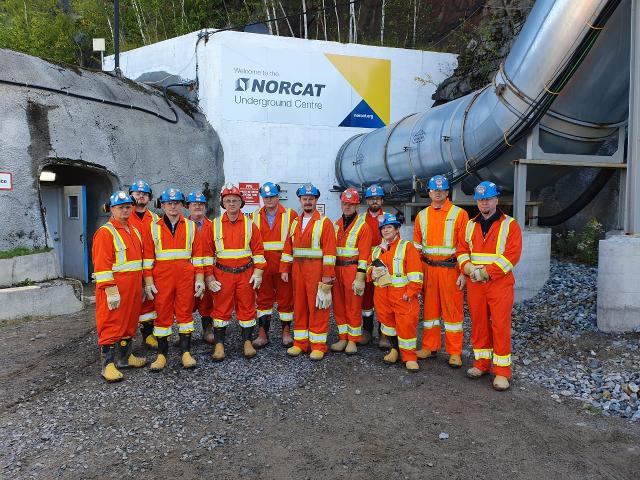
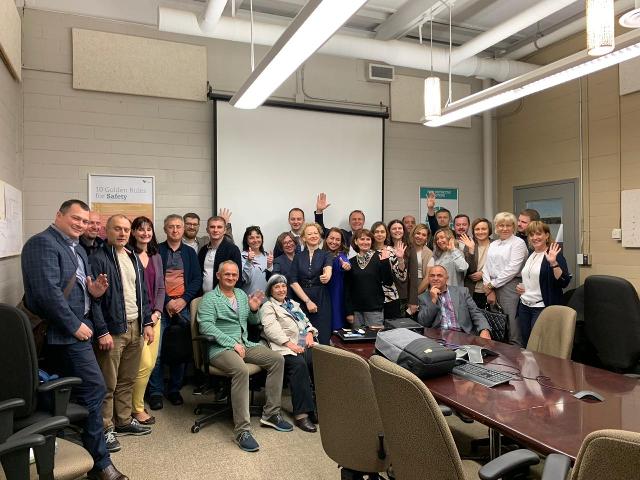
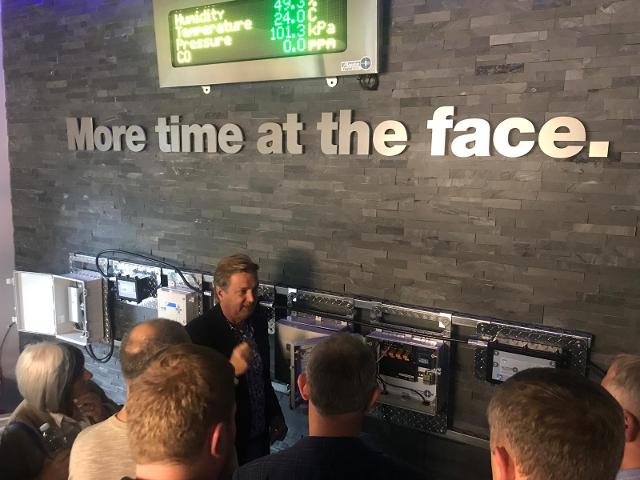
At a warm welcome reception organized by Canadian colleagues and Sudbury City Hall Mayor Brian Bigger met the group of Kazakh and Russian miners and shared his experience of restoring ecology in the region, spoke about sustainable development initiatives by mining companies operating in the Sudbury region and support for mining industry and close cooperation with regional authorities. The visitors were greatly impressed by how the environment was successfully restored in a region that saw acid rains 50 years ago due to nickel production and emissions. The outskirts of this mining town, formerly reminiscent of “Lunar landscape” were used by NASA to test equipment for the Moon landing. Now the ecology of Sudbury can be admired and the city and its surroundings are green.
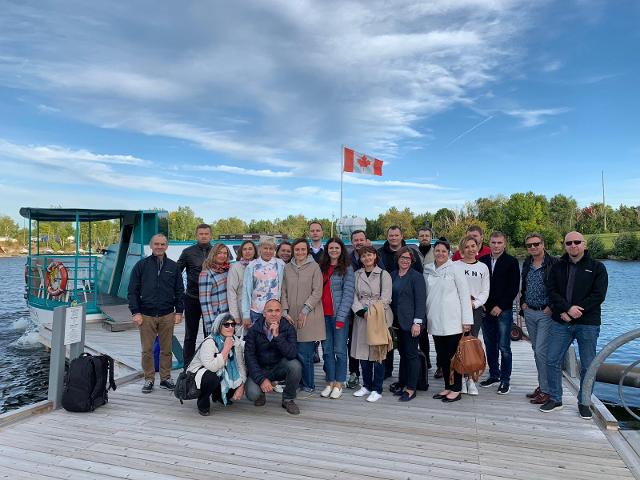
Part of the group visited the Porcupine mine and familiarized themselves with underground gold mining.
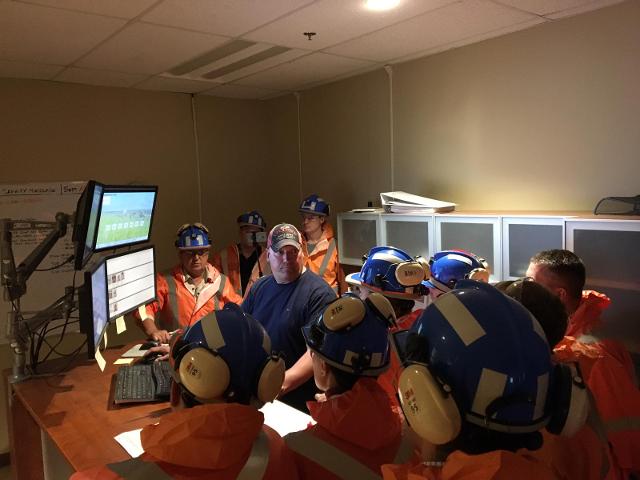
Porcupine Mine is a unique enterprise where mining operations are carried out both in open pits and underground. GOLDCORP implements a 5-year strategy 20/20/20, which comprises a comprehensive programme of cost reduction: in the period from 2017 to 2021 the mine has plans was to annually reduce costs by $250 million and this target was successfully met in 2017 and 2018. The main success factors are improving energy efficiency, reducing costs, introducing autonomous drilling rigs (manufactured by Epiroc), reducing accident frequency, improving operational safety, and introducing the most advanced search and rescue equipment in an emergency.

Mining in the world of innovation: new technologies to ensure high profitability of mines. Advanced tailings solutions. Technical visits to Neves Corvo and MATSA mines
Lisbon – Neves Corvo – Aguas Tenidas – Seville (Portugal-Spain) September 16-21, 2019
The practical implementation of the most advanced technical solutions for tailings thickening and a compacting compact tailing dump was demonstrated to a delegation of leading experts and managers of mining companies of Russia and Kazakhstan in Portugal at the Neves-Corvo ore processing plant of the Canadian company Lundin.
The project and equipment were delivered by Outotec, a Finnish company, the world leader in tailings and water management. Thanks to this technology, the need for tailings areas is reduced significantly. Outotec’s head of hydrotechnical solutions and tailings utilization Arturo Gutierrez del Olmo spoke in detail and demonstrated the technologies introduced at the mine to eliminate the extension of the dam and tail slopes due to dewatering of tailings, and Outotec equipment for tailings thickening and filtering.
During the second technical visit to Spain, the seminar participants visited the ore processing plant of the Swiss-Abu Dhabi company MATSA, where they got acquainted in detail with the norms and regime of industrial safety, technical equipment and the operation of an ultramodern enrichment plant with its fully automated control room, sample preparation laboratory and organization work of a chemical analytical laboratory.
Among the participants of the event were specialists of Daltsvetmet, Eurochem-Usolsky Potash Plant, IMC Montan, AGD Diamonds, Uralkali, Sary-Kazna and Eurochem-Project. In the evening, free from work at the seminar, the participants took a swim in the Atlantic Ocean and got acquainted with the history of Lisbon and Seville.
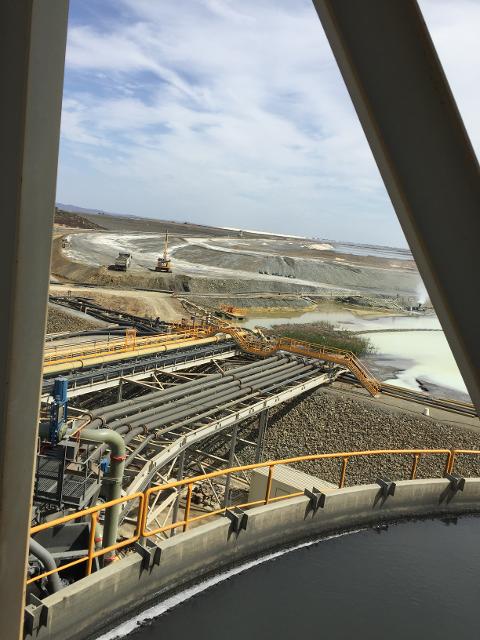
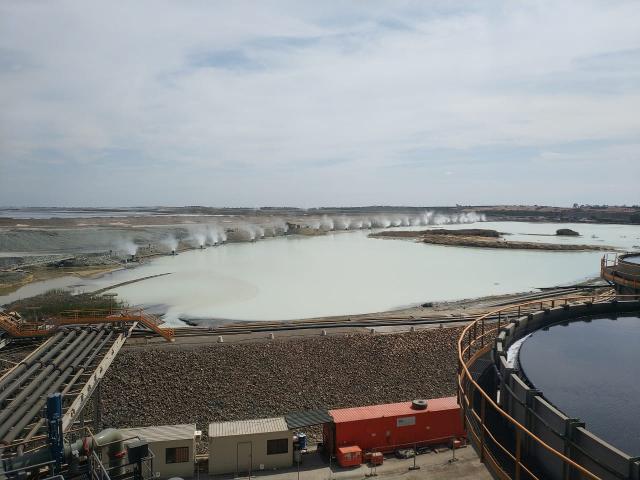
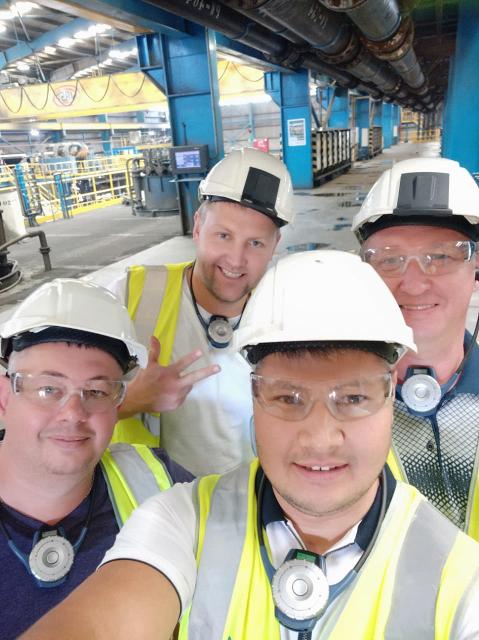
“Drilling in the world of digitalization – innovative technologies and cost reduction during drilling and well operations” September 9-13, 2019 Hanover-Celle-Hanover
Digital ecosystems for well construction, optimization of drilling and production through digitalization and navigation systems for ultra-deep formations were the subjects of a detailed discussion in the program of technical visits organized by the Trans-European Center in September 2019 in Hannover and Celle (Germany).
The seminar was attended by a delegation of managers and leading experts of oil and gas and drilling companies from Russia, Kazakhstan and Uzbekistan, who also attended the Drilling Celle 2019 international congress on drilling technologies (with simultaneous translation into Russian) in Celle.
It was here that in 1859 the first oil field in Europe was drilled. Now in Celle Hanover there is a cluster of oilfield services companies and manufacturers of innovative equipment for the oil industry.
The delegation visited the technology and production centers of Baker Hughes, Goes Well GmbH and Weatherford Oil Tool GmbH. Among the participants of the event are heads and specialists of LUKOIL and its subsidiaries in Perm, Astrakhan, Kogalym and Usinsk, RITEK, Eriell Group, YugGazEnergia, Kazmunaygaz-Burenie, Burgylau and SibBurMash.
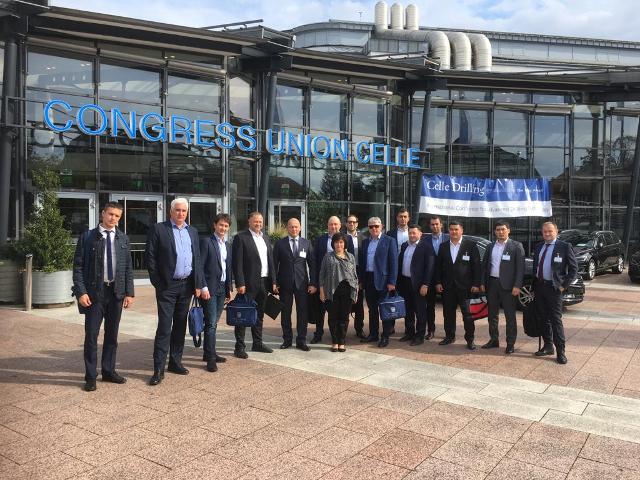
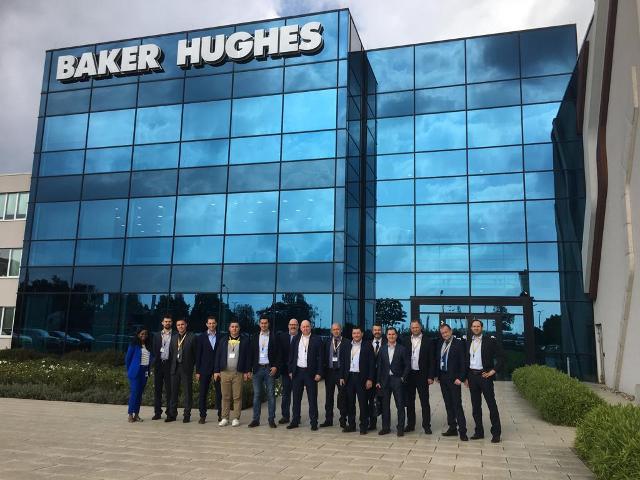
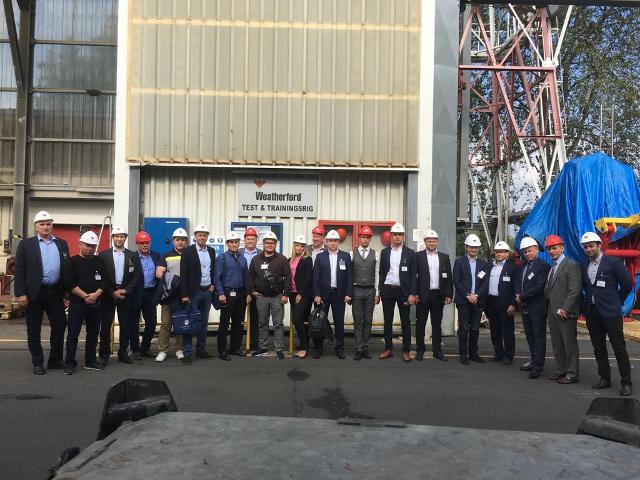
Experience of leading metallurgical companies in the field of HSE. Economic and social benefits from the implementation of high standards of industrial safety. August 19-24, 2019 England
A group of managers of the leading Ukrainian metallurgical holding Metinvest studied and analyzed in detail the industrial safety standards that have been implemented at metallurgical and other industrial enterprises in the UK.
Ukrainian metallurgists visited the Normanton Steel Plant in Middlesborugh and the laboratory complex of the Technological Institute of Materials Science, where they got acquainted with the practical design of the safety system and exchanged practical experience with the plant’s specialists.
The seminar was also addressed by representatives of DNV-GL, the European Center for Process Safety (Rugby) and DuPont Sustainable Solutions. 3M / ScottSafety British specialists demonstrated the latest developments and safety equipment when working at heights, and Schenck Process (Germany) talked about the latest technological innovations in the fight against dust and air pollution in industrial premises. The program of the seminar, technical visits and Q&A sessions was informative and practical.
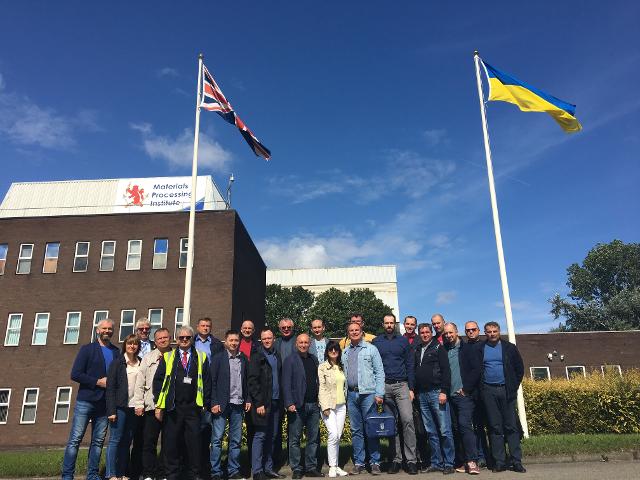
Middlesborough
June 24-28, 2019 Stavanger (Norway) Intelligent field as a method of increasing production and optimizing costs. Digitization of drilling processes.
A group of executives and specialists from leading Russian oil and gas companies, including Lukoil, Rosneft and Gazpromneft, studied the practical experience and economic effect of implementing solutions for digitizing and automating the drilling and production of hydrocarbons on the continental shelf of the North Sea. Baker Hughes General Electric, Cognite, Weatherford, Exebenus, FutureOn, Kongsberg Digital, Wellit, MHWirth, and others presented their innovative solutions for digitizing key production and business processes to Russian oil companies.
The workshop participants also visited the Norwegian Oil and Gas Research Center NORCE and the experimental Ullrig drilling rig (drilling depth 2.3 km), where robots are being introduced to fully automate the connection of pipes during descent.
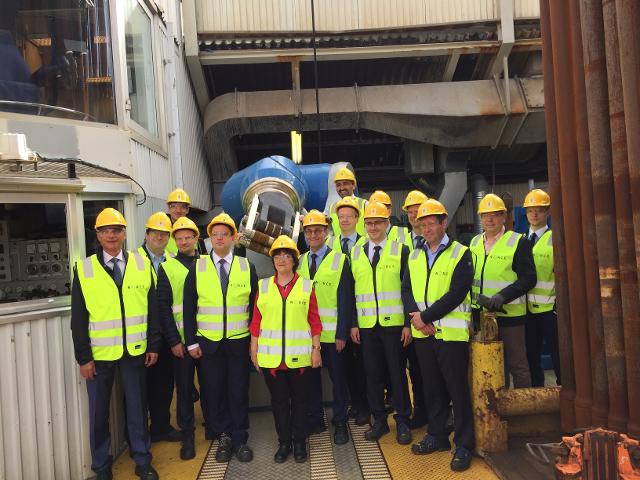
Photo: workshop participants at the working level of an experimental Ullrig drilling rig
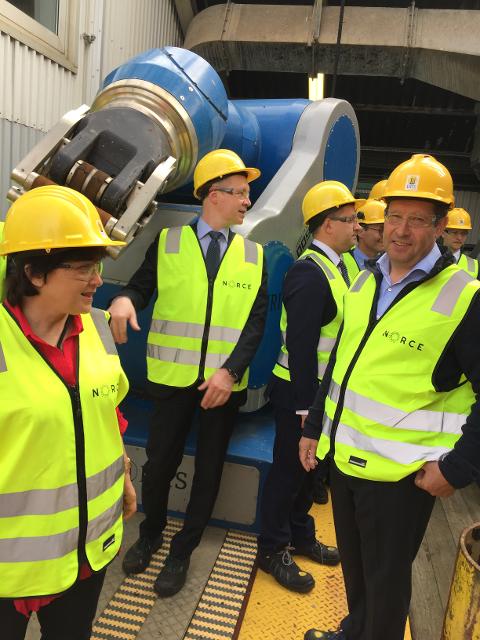